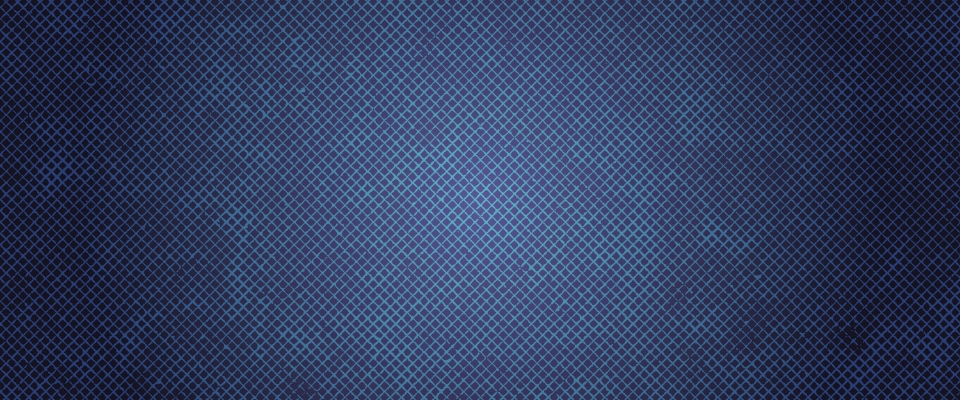
Advanced Solutions for the Pharmaceutical Industry: Serialization, Cartoners, Filling Systems and Visual Inspection
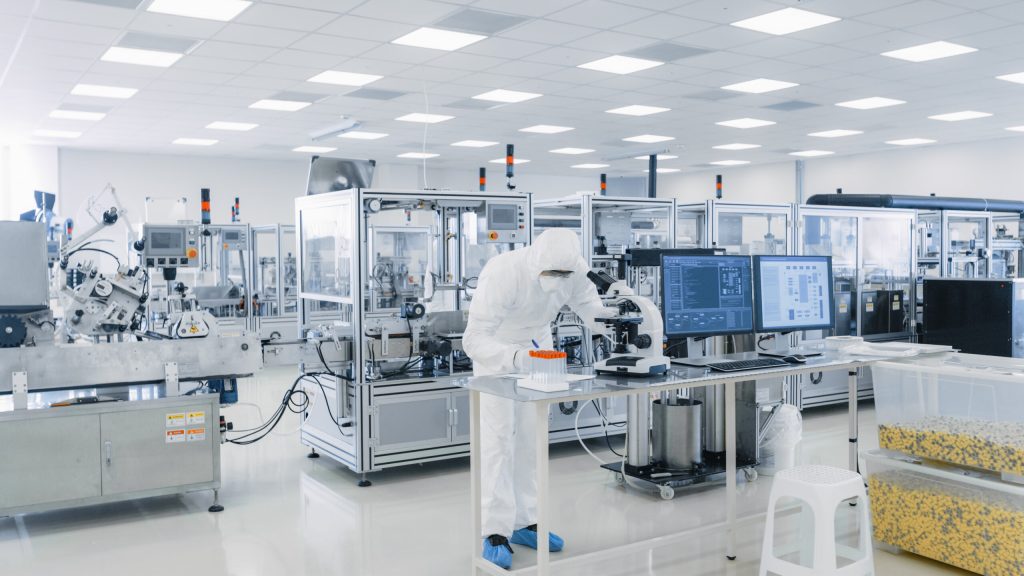
Serialisation and aggregation
For only a few years, the so-called “anti-counterfeiting” Directive of the European Union and Regulation (EU) 2016/161 of 02.10.20215 have been in force., and the resulting obligation for serialisation, we have been able to prove that our serialisation approach brings tangible benefits to users and has a positive impact on quality and ease of production:
- uniformity of the solution (no additional components or separate solutions for other levels),
- ease of integration with third-party systems (MAH, CMO, EMVO, KOVAL),
- full control of users and templates by the supervisory system.
The extension of Introl Automatyka to the broader pharmaceutical industry, allows us to offer, a wide range of serialisation and aggregation devices. Whether a manual, semi-automatic or fully automatic device is required, based on expected throughput and available space, we adapt and/or design the appropriate device(s). Thanks to such a flexible approach, we can be independent of any particular equipment supplier, this also allows us to select the best solution for our customers based on specific local requirements. Undoubtedly an important aspect of working in such a rapidly changing environment, is support and access to application engineers with both relevant experience and extensive communication capabilities in an international environment. Our team of support engineers, provide all the necessary information and services on an ongoing basis that allow our customers to adapt smoothly to changes, expand functional and communication capabilities and, most importantly, run their day-to-day operations with peace of mind.
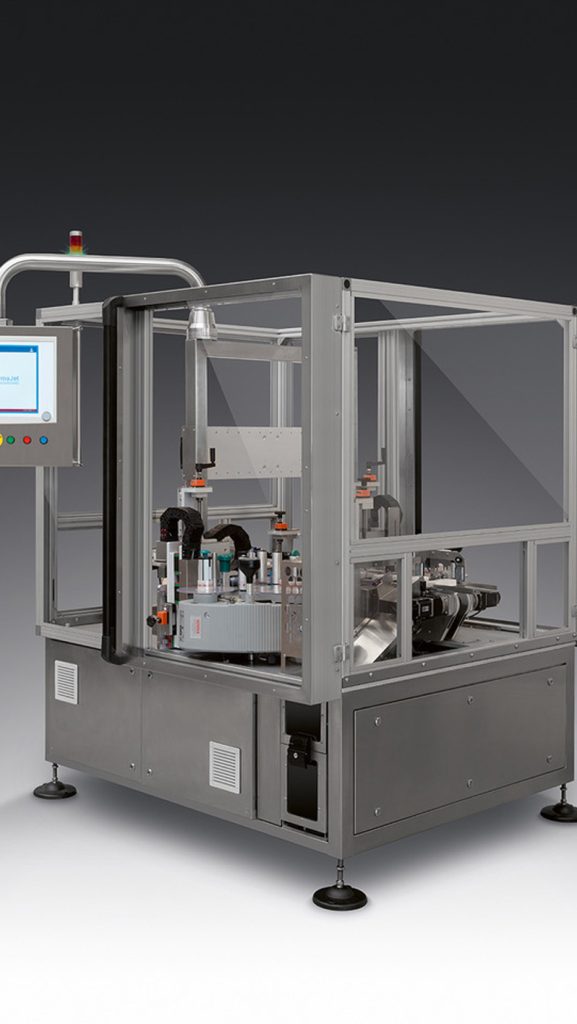
Siempharma bulk cartoners
Depending on the volume of production, the amount of space available and investment opportunities, it may be advisable to use semi or fully automatic equipment. The main difference lies in the preparation and collection of the finished collection packs. With semi-automatic equipment, the operator places the carton unfolded and glued from underneath. Through a pneumatic system actuated by the operator, the handle rotates 90° and starts the process of automatically filling the carton with whole layers of wrappings. Once the filling operation is complete, a filling sensor initiates the return of the case pack to its original position and the transfer of the case pack to a roller conveyor, where again the operator picks up the carton, seals the top and transfers it manually to palletisation. In the case of automatic equipment, the process of unfolding, closing, gluing and labelling of the master cartons takes place automatically. In addition, in the palletising area, cartons can be automatically transferred to pallets using robotic systems.
Benefits of the machine:.
- automation and acceleration of the case packing process,
- the possibility to control the contents and the full aggregation of pre-packaging data,
- wide adaptability of the equipment according to the type of packaging (bottles, cartons).
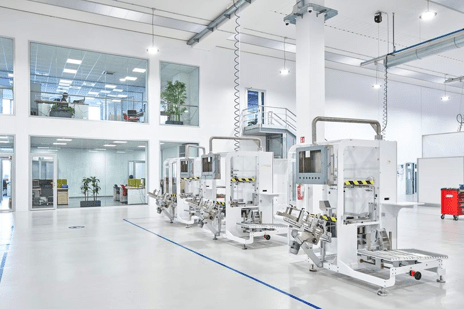
Counting, blistering, filling: effective methods in the pharmaceutical industry
Siempharma offers machines for the inspection of liquid, lyophilised or powdered products stored :
- in ampoules
- in vials
- in carpules
- in bottles
- in ampoules and syringes
The solutions can handle 100 to 300 pieces per minute..
A wide range of inspection technologies:
- foreign reflective and non-reflective particles,
- fibres,
- glass,
- correct filling level,
- checking tip/cap (shape, height, black spots, position of cap),
- colour control of the ring/cap,
- product colour,
- print control;
- defects in glass elements,
- piston check (for cartridges).
We offer:.
- scales with the function of rejecting defective products – capacity up to 300pcs/min,
- automatic blister machines,
- automatic monobloc counting and capping machines.
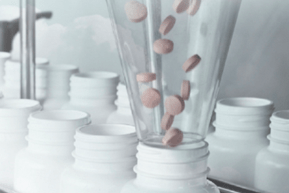
Liquid filling machines (monoblocs)
Machines and monoblocs for the filling of packaging with liquids and their subsequent closing/closing are the result of years of experience with the design of this type of equipment. They are prepared to meet the needs of a market requiring high productivity, ease of format change and compliance with GMP standards. The innovative design of the various workstations allows for the correct application of laminar flow in the work area and quick format changes that can be easily repeated. The filling system (using volumetric or peristaltic pumps) is highly accurate thanks to the high level of technology used. Easy cleaning and inspection is guaranteed thanks to the separation between the package transfer area and the machine base. Siempharma’s solutions are designed to meet the different filling and capping criteria required by the pharmaceutical, nutraceutical and cosmetic sectors. Placement of the closer/closer can be performed by means of a fixed forced movement, raising and lowering or robotic positioning. In the case of closers, initial tightening and final tightening is carried out using dedicated closing heads characterised by electronic torque control. The monoblocks can be installed with up to three different locking units, suitable for guaranteeing the use of all the different types of caps used in the industry (with child protection, with opening protection, etc.). The reduced dimensions of these machines, their flexibility and their innovative design mean that they can be easily integrated into complete as well as existing packaging lines.
Benefits:.
- space-saving production space,
- full control over tightening force,
- automation and acceleration of the packaging process,
- easy cleaning and maintenance,
- user-friendly and intuitive touch-screen HMI for quick learning and fast configuration,
- compliance with CFR21 part 11/EU Annex 11 and INDUSTRY 4.0 standard
- Design, manufacture and ergonomics in accordance with GMP standards,
- CE certified.
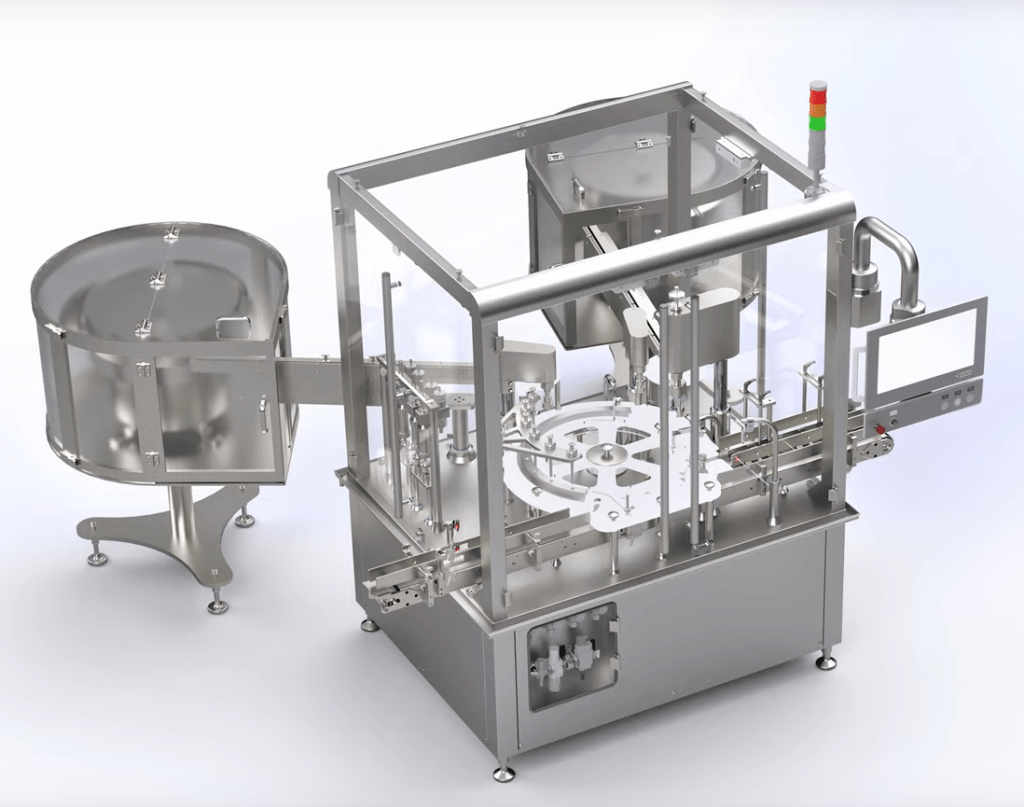
Unit cartoners
Depending on the volume of production, the amount of space available and investment opportunities, it may be advisable to use semi or fully automatic equipment. The main difference lies in the way the product is placed in the unit packaging (carton). With semi-automatic devices, the operator places the product in the wrapper, while the leaflet is placed automatically. The printing on the carton (LOT, batch number, expiry date, etc.) can be carried out by means of a so-called coding unit, which embosses the relevant data on the carton using fonts, or by means of the wide range of available printers. In the case of automatic cartoners, the whole process is continuous and the role of the operator is limited to the supervision of the machine (loading of the wrappers and leaflets). In addition, the process of changing the format is fully automatic without the need for a assistant technician.
Benefits:.
- automation and acceleration of the case packing process,
- wide adaptability of the equipment according to the type of packaging,
- large available space in the product loading area,
- cantilever design with clear separation between the mechanical part and the product handling area,
- single cover for convenient and quick access,
- easy cleaning and maintenance operations,
- user-friendly and intuitive touch-screen HMI for quick learning and fast configuration,
- compliance with CFR21 part 11/EU Annex 11 and INDUSTRY 4.0 standard
- Design, manufacture and ergonomics in accordance with GMP standards,
- CE certified.
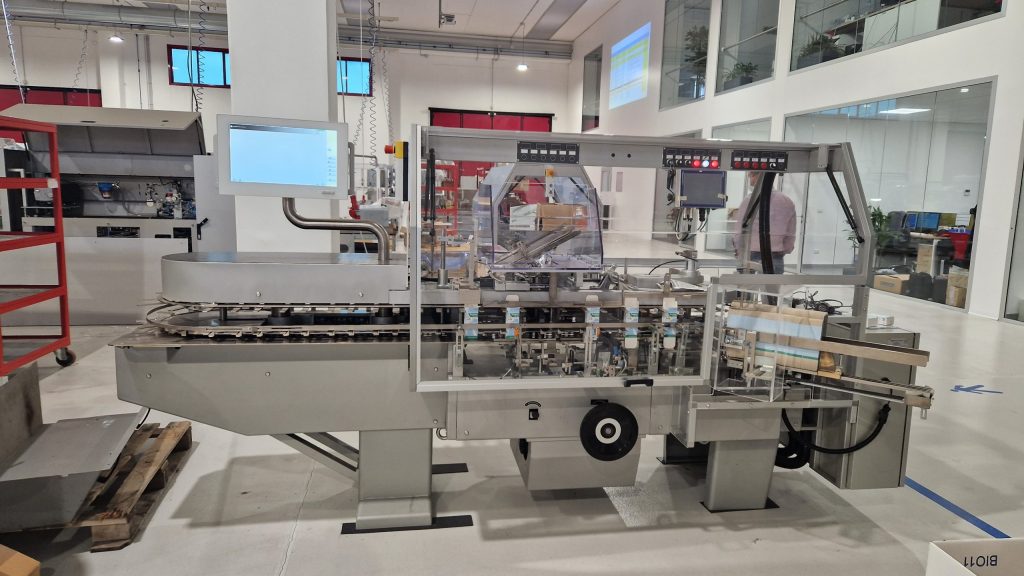
Synergy system
In order for measurements of environmental conditions to be realised under conditions of multiple GxP practices, several basic conditions must be met:
- high quality of sensors enabling accurate and reliable measurements,
- integrity and data security on multiple levels,
- full documentation validation, and security of data on multiple levels
- extensive notification of alarm events to users.
The Synergy system offered by IMC fulfils all of the conditions described above, which has resulted in a wide range of users in the areas of production and pharmaceutical distribution. The combination of excellent, in-house radio technology together with top-class measuring sensors from world-leading manufacturers (i.e. E+E Elektronik, Vaisala) allows the best possible selection for the existing measuring conditions which guarantee the highest possible accuracy regardless of the measured value (typically temperature, humidity, CO2, differential pressure). Software based on an engine running on a central server (possible on-premise or in the cloud) and user access via web browser, combine security of data collection and management and ease of access. Intuitive screens and visualisation flexibility make it easy to view data even from multiple remote locations and detect potential problems.
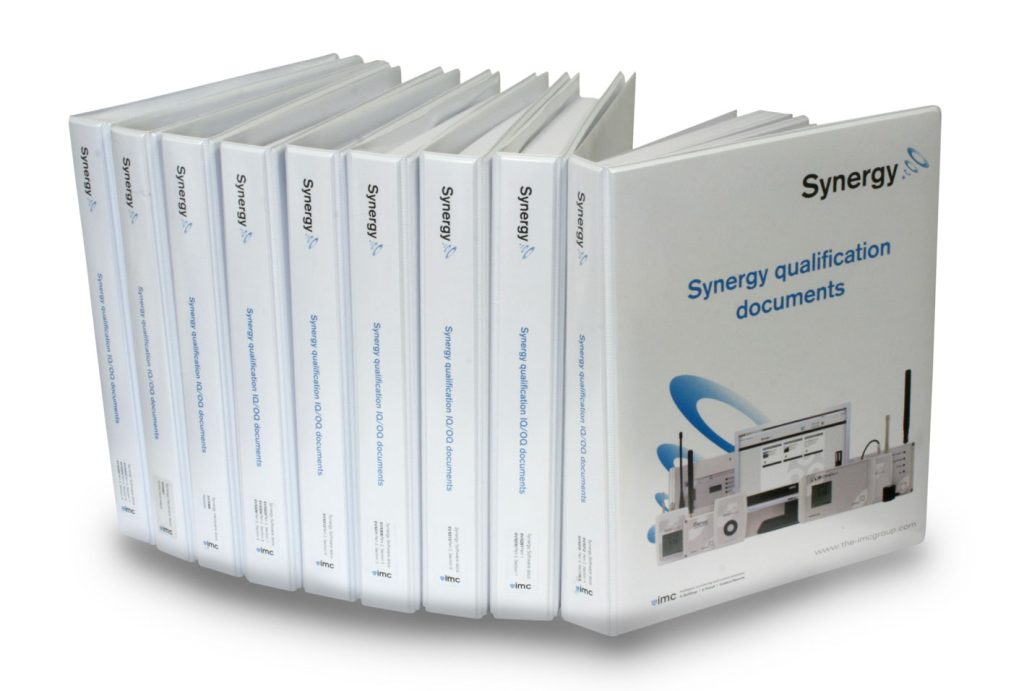
Electronic batch recording (EBR)
Errors can be prevented in advance or eliminated altogether. Electronic batch recording systems are designed not only to improve the quality of the production process but also to increase its efficiency in a real way and avoid unnecessary costs. In terms of process data, continuous access is possible and early action can be taken on any adverse events detected in the process. The user is provided with precise instructions for each workstation, predefined operations and safety guidelines. Reports, documentation and other development support tools, are created in real time, in parallel with production. This type of electronic recording reduces the time taken to collect data, and analyse it, by 70% compared to paper documentation.
The advantages of electronic batch record systems can also be seen at workplaces. The EBR System (Electronic Batch Record) allows automation of the perusal and completion of paper work logs of equipment and records from documenting the progress of the manufacturing process without making changes to the process itself.
The main advantages of the EBR System include:.
- real-time checking of results,
- repeatability of production batches,
- shorter training times for operators,
- reduced costs.
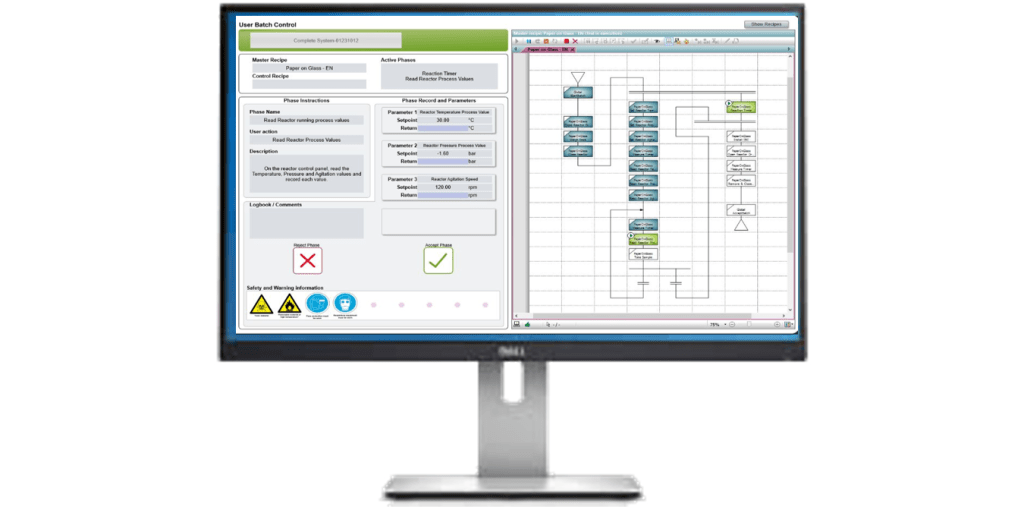
Vision control equipment
Automatic vision inspection directly translates into increased quality of the final product. Vision devices make it possible to inspect the unit product before packaging (tablet, ampoule, vial), during packaging (completeness of blister and carton, accounting of quantity), or during labelling (correctness and completeness of imprints). From individual verification components (i.e. camera or video scanner) to complete devices performing additional functions, i.e. verification of leakage and labelling. Extensive self-learning capabilities and artificial intelligence systems enhance the ability to detect defects and abnormalities, which, combined with high performance, produces results that are difficult to achieve during inspection by the human eye.
Main benefits of using Vision Devices:.
- reduction of contamination control costs in
packaging, - increased production capacity,
- increasing the efficiency of the production process,
- reducing bottlenecks in the manufacturing process,
- increased reliability of vision inspection,
- reducing the risk of batch recall.
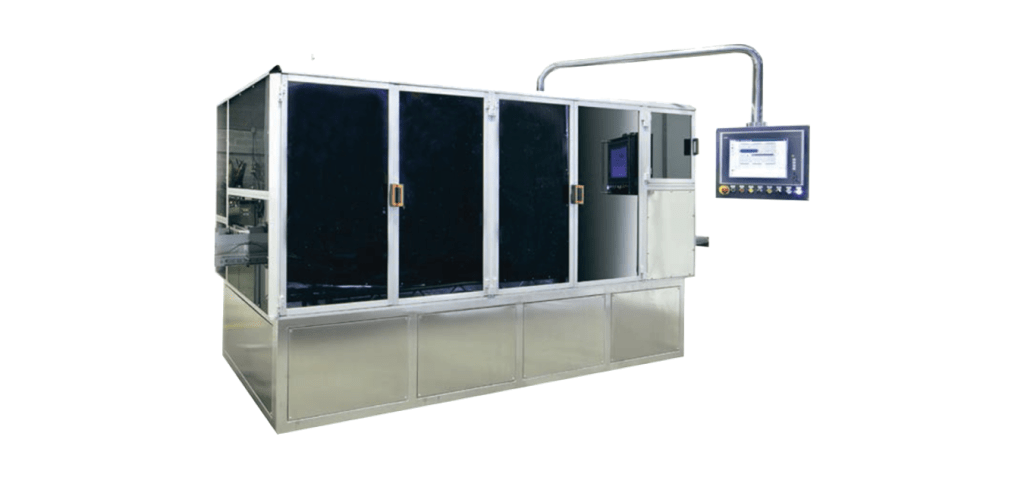
Robots
Our range of industrial robots for the pharmaceutical industry combines high-end products together with the experience of our specialists in working in environments regulated by EU GMP. Whether the intended workplace is the packaging area or the sterile area in the manufacturing process, we will select the best solution using a wide range of cooperative equipment (cobots), SCARA robots, parallel kinematics (Delta) or 6-axis robots operating in a clean air zone. Our solutions ensure high precision and repeatability, have the ability to operate in hard environmental conditions, without the constraints of contact with toxic substances. These capabilities allow a wide range of applications for robotic devices, particularly where the work involves a high risk to worker health.
- If you need a automated solution that works with pharmacy and precision, which requires the highest speed, precision and accuracy, be sure to try the robots SCARA and Delta series.Benefits of the device:.
- high speed,
- relatively long range,
- precision of movement,
- increased production capacity,
- increasing the efficiency of the production process.
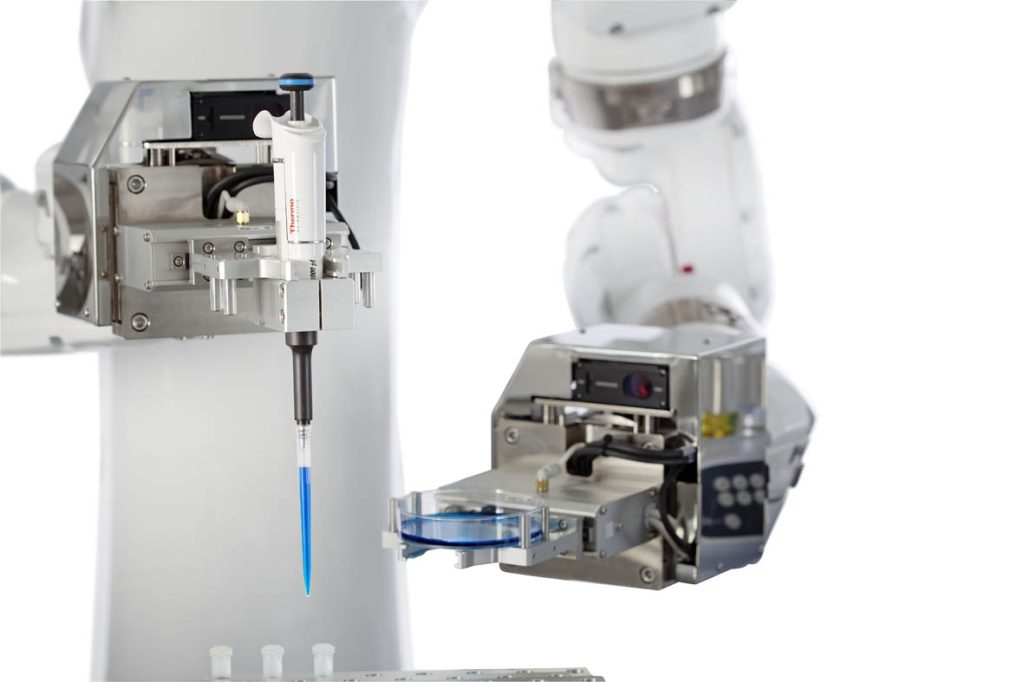