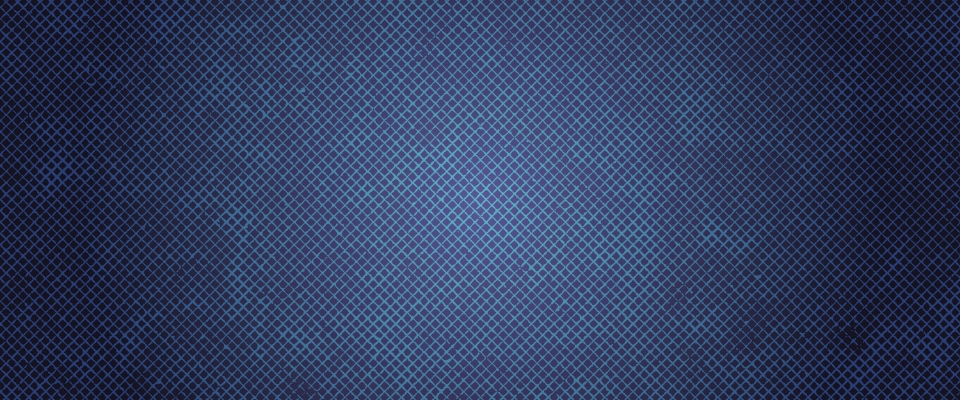
News
What is Cogeneration?
Cogeneration is the process in which the heat generated during electricity production is used for other purposes, such as heating buildings or for industrial processes, for example, in trigeneration, where it is used for cooling. Cogeneration engines are a key component of such systems, and their efficiency directly impacts cost savings and environmental protection. With proper management, cogeneration can significantly reduce operational costs and carbon dioxide emissions.
Why is Prevention Crucial?
Preventive maintenance in cogeneration engines is essential for several reasons:
-
Increased Operational Efficiency
Regular maintenance and inspections help keep engines in optimal condition, which directly affects their energy efficiency. Keeping the engine in good technical condition can significantly reduce fuel consumption and pollutant emissions. -
Reduction of Operating Costs
Early problem detection and regular inspections can prevent costly breakdowns. Unplanned downtime can result in substantial financial losses and disruptions to production. -
Enhanced Safety
Proper prevention increases workplace safety for both personnel and the equipment. Regular checks help identify potential hazards. -
Extended Equipment Lifespan
Prevention is key to extending the service life of cogeneration engines. With proper maintenance, engines can run much longer, translating to better returns on investment.
Key Preventive Measures
-
Regular Technical Inspections
Systematic engine inspections should cover key components such as the fuel, cooling, oil, and exhaust systems. Good practices involve performing inspections according to the manufacturer’s recommended schedule. -
Proper Maintenance
Maintenance should include all critical engine systems, such as:- Oil system: oil changes, filter replacements, and oil sample analysis
- Cooling and ignition systems, knocking combustion system, and fuel mixture regulation system
- Monitoring key components like turbochargers, generators, and lubrication systems to ensure proper operation and avoid premature wear or failure
Regular checks help detect potential issues early, enabling quicker repairs and minimizing the risk of costly breakdowns.
-
Monitoring Operating Parameters
Utilizing modern real-time monitoring systems allows continuous tracking of critical parameters such as knocking combustion, temperature, pressure, and vibration levels. Early detection of irregularities enables prompt action and prevents more severe failures. -
Fuel Quality Management
Fuel quality is crucial for the efficiency of cogeneration engines. Regular gas analyses and proper purification (especially for biogas) help prevent issues related to contaminants that can cause combustion chamber deposits, corrosion, and reduced efficiency. High-quality fuel also ensures stable system operation and reduces the risk of failures, contributing to the long-term reliability and profitability of cogeneration systems. -
Staff Training
Proper staff training is essential, as employees are responsible for prevention and analyzing engine performance. Understanding operational principles and responding quickly in emergency situations can significantly improve the device’s safety and efficiency.
Prevention in Cogeneration Engines – The Key to Efficiency and Longevity
Cogeneration engines form the foundation of modern energy systems, enabling simultaneous production of electricity and heat. To ensure these engines operate efficiently for many years, it is essential to implement effective preventive measures. This article has discussed the importance of prevention and key actions that contribute to engine longevity and optimal performance.
Let’s Collaborate!
If you want your cogeneration engines to operate at full efficiency for many years, we invite you to collaborate with us. Our company offers comprehensive solutions for prevention, maintenance, and monitoring to help keep your energy systems in top condition. With our services, you can count on minimized operational costs, enhanced safety, and long-term reliability of your equipment.
Invest in preventive maintenance today to secure a future free from breakdowns and unexpected costs. Contact us to learn how we can work together to achieve success in managing your cogeneration engines!